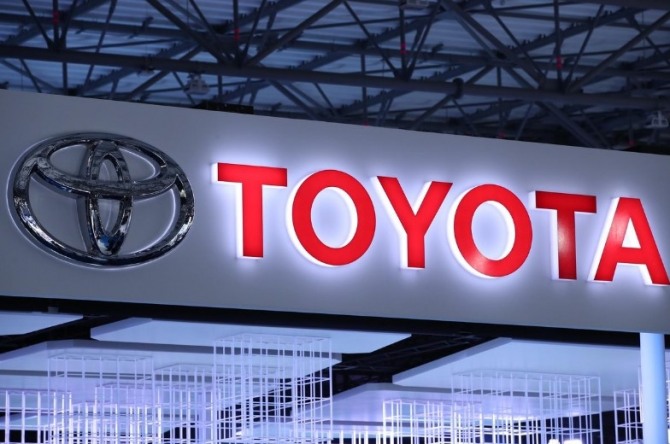
서로 다른 배터리 소재를 실은 이송 팔레트가 상하 두 개의 레일을 고속으로 이동하다가 상대 속도가 제로(0)이 되는 동기화 지점에 도달하면, 눈에 띄지 않을 정도로 빠른 속도로 소재를 고정하고 있던 위쪽 팔레트의 '발톱'이 풀리고, 절묘한 타이밍에 아래쪽 팔레트의 발톱이 소재를 받아 겹쳐진다.
토요타 사다보 공장의 한 구석, 전고체 배터리 개발 현장. 마치 마법처럼 움직이는 발톱을 이용한 양산 방법을 시험하고 있었다.
2027~2030년 실용화를 목표로 개발 중인 전고체 배터리는 기존 전해액계 차량용 배터리보다 성능이 크게 향상되어 EV의 항속거리를 1000km 이상으로 늘릴 수 있다. 이 첨단 기술은 배터리를 구성하는 양극재, 음극재, 고체 전해층이 빈틈없이 밀착되는 것이 제조상의 큰 과제다.
양산에는 소재에 손상을 주지 않고 고속, 고정밀도로 배터리 소재를 적층하는 난제가 있지만, 일본 전통의 가라쿠리 기법을 자동차 제조에 적용한 토요타 방식이 이를 해결해 나가고 있다. 불필요한 동력이나 배선을 늘리지 않는 단순한 구조는 생산의 안정성에도 기여한다.
한편, 엔진 부품 등 주조품을 취급하는 아키치 공장(아이치현 미요시시)에서는 대형 차체 부품을 알루미늄으로 일체 성형하는 기가캐스트 설비가 가동되고 있다.
로봇이 고온으로 녹인 알루미늄을 금형에 붓고, 4000톤의 압력을 가하는 장비가 압력을 가하면, 지금까지 수십 개의 판금 부품을 사용해 몇 시간씩 걸리던 차체 부품이 단 3분 만에 완성된다. 이 신공법은 테슬라가 실용화한 혁신 기술로, 토요타의 도입은 '짝퉁'이라는 비판을 받기도 한다.
이에 대해 토요타는 "우리가 상상도 할 수 없는 제조를 해내서 솔직히 놀랐다. 새로운 선택지를 벤처로부터 배우고 도전하고 있다"(생산 부문 총괄하는 신고 카즈아키 전무)고 인정하고 있다.
다만, 기가캐스트의 실용화에는 타사 대비 20%의 생산성 향상이라는 '테슬라를 뛰어넘는' 목표가 설정되어 있다. 이를 실현할 수 있는 것은 '장인'이라는 숙련공의 기술과 디지털 기술을 결합한 토요타의 제조력이다.
장비가 거대해지는 신공법에서는 보통 크레인 등을 이용한 정기적인 금형 교체 작업에 24시간 정도 소요된다. 이를 토요타는 단 20분 만에 실현한다. 창업 이래 쌓아온 장인정신으로 독자적인 형태의 금형을 개발했다. 시제품은 장치 기반의 범용 금형과 제조품 형상의 전용 금형을 분리하는 구조로 전용 금형의 자동 교환을 가능하게 했다. 이는 현재 '토요타만이 할 수 있는 것'(신고 씨)이라고 합니다.
또한, 장인 특유의 경험과 품질 체크 포인트를 반영할 수 있는 독자적인 디지털 분석 기술로 불량품 발생을 억제하여 총 20%의 작업 낭비를 줄여 생산성 향상을 꾀한다. 공법은 같지만, "공정의 낭비를 줄여나가는 생각은 다를 것"이라고 공장 담당자는 테슬라와의 차이점을 지적했다.
신생 업체인 테슬라나 비야디는 엔진차 생산기술에 얽매이지 않고 처음부터 EV에 최적화된 개발 및 설비 투자를 할 수 있었다. EV로 앞서가는 테슬라 등을 추격하는 입장인 토요타로서는 엔진차의 기존 생산설비 유지가 발목을 잡는다고 보는 시각도 있다.
하지만 토요타가 이번에 공개된 생산기술은 오랜 자동차 제조를 통한 기술 축적과 불필요한 작업을 줄이는 노력 등 현장 역량이 오히려 후발주자들과의 차별화를 위한 발판이 될 수 있다는 가능성을 보여준다.
노정용 글로벌이코노믹 기자 noja@g-enews.com